EDM Encore 6BR Varminter
A Wolf in Sheep's Clothing with .2 MOA Accuracy
Other Guns of the Weeks > Though versatile, compact, and reliable, the Thompson/Center Encore is not a gun one would instinctively associate with state-of-the-art technology or truly exceptional accuracy. Well get ready for a paradigm shift. Richard VanH's 6BR Encore raises the accuracy bar for break-open rifles. This rig may be plain on the outside, but it's seriously tricked out on the inside. Richard's Encore features a chamber exactly matched to his loaded ammo--a chamber cut with an electrical spark, not a conventional reamer. With a precisely-machined lug and oversized hinge-pin, lock-up is ultra-tight. Encore/Contender guru Mike Bellm (who knows as much about Encores as anyone on the planet) performed a complete action/trigger job. So here you have a truly exceptional Encore, one with 0.2 MOA accuracy to match its switch-barrel versatility.
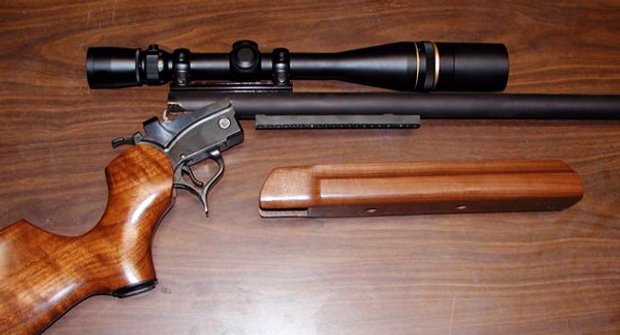
We've long been intrigued by the T/C break-open, switch-barrel firearms, but when Richard VanH told us about his new 6BR Encore, we knew we'd found something very special indeed. Richard noted that the first five-shot group from the gun went into just 0.207"! That was with virtually no load development and plain-vanilla 75gr V-Max bullets. The rifle also has some exotic technical features. Richard explained: "The gun actually is very interesting. A new, patented EDM (Electro Discharge Machining) process was used to cut the chamber. The chamber is made to your loaded dummy round instead of the round being loaded to suit the chamber. Target shooters and accuracy buffs will find it very interesting. There is no reamer. So far I'm amazed with the accuracy. It shoots as well as a full-tilt benchrest rifle I had built by a very well-known top BR smith. The Encore is a very inexpensive nail-driver that was easy to build."
In putting together this project, Richard started with modest expectations--he certainly didn't expect a quarter-MOA tack-driver. He already owned an Encore action, equipped with a .50-Caliber muzzle-loading barrel, as well as a .270 Win barrel for deer hunting. But he wanted to use the Encore for varminting as well, something with excellent accuracy. He chose the 6BR cartridge for its inherent accuracy, low recoil, and high-quality components. The barrel assembly was crafted by Mike Sirois of On Target Technologies, LLC. in New Hampshire. Mike used his innovative, patented EDM process to cut the chamber after measuring dummy rounds supplied by Rich. Encore/Contender expert Mike Bellm of Bellm TCs, Inc. provided some key component upgrades (heavy-duty lock-springs and oversize hinge-pin), and performed a masterful action/trigger job. Richard says "Bellm did a superb job. The trigger is now under 12 ounces, and very smooth and crisp." The last addition was a wide, flat benchrest-style forearm from Old Georgia Jim, a specialty supplier of T/C Contender and Encore grips and fore-ends.
Richard's unassuming Encore may be one of the most accurate of its breed ever built--testimony to careful craftsmanship and component selection. Richard is still trying out various bullets and load combinations, but he says that all the bullets he's tried (65gr V-Max, 75gr V-Max, and 80gr Berger) have shot well in the 12-Twist Douglas barrel. Much of the accuracy can be attributed to the ideally-fitting chamber and a barrel lug that was machined and fitted to very tight tolerances. Richard tells us, "the beauty of the EDM chambering method is that you don't have to mess around trying to get brass to fit the chamber. With break-open guns, correct case-sizing and headspace is critical to good accuracy and reliability. Normally a guy will have to fiddle around with his brass and dies to get the right headspace. With an EDM chamber, maintaining the correct headspace is easy, because the chamber is dimensioned to fit the brass you produced with YOUR dies."
Richard, a law enforcement officer, first got to shoot the Encore after returning from duty in Louisiana, as part of the Hurricane Katrina response force. Here is Richard's initial range report to Mike Sirois:
I just got back from flying rescue ops over in New Orleans. I promised you honest feedback on this barrel you just sent me, so here goes...
First, I liked the finish. When I slipped the hinge-pin in place, I thought it should have been a bit snugger. It wasn't loose but not as tight as I wanted. I could push it through with my fingers and I was expecting to oil it and knock it through with light taps. I then measured the barrel to frame breechface clearance and it was less than .001". Fantastic! Next was the chamber check. It was absolutely, perfectly concentric and the cases seated to less than .0005" from flush! So my headspace was perfect.
I took some untouched out-of-the-box Lapua brass with AA 2230, and seated Fed 205M primers. Then I loaded 75gr V-max bullets .001" into the lands. I thought I would load the serious benchrest bullets after fire-forming and barrel break-in. I went to the public range and cleaned the barrel with some Butch's BoreShine and fired two for a little "seasoning" and to zero it in. Then I re-cleaned and shot for group and load development.
The range officer, looking through a 40X spotting scope, didn't see shots two and three. I just grinned because I know what a good 6BR will do. Shot #5 opened the group to a measured 0.207", for the first group right out of the box! V-Max bullets no less. I couldn't be happier! So now I have a $3000.00 6BR that a famous gunsmith and benchrest Hall of Famer built for me that's going up for sale. They shoot identical! | |
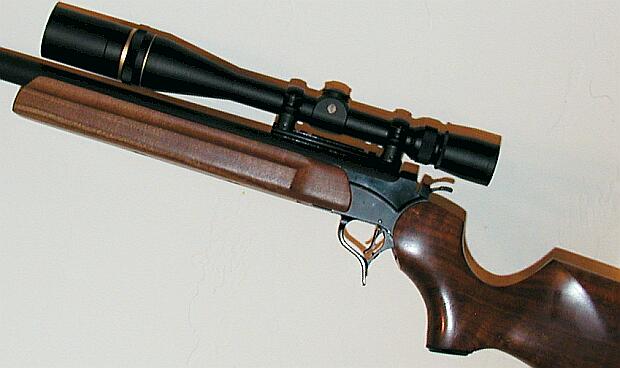
We are fortunate that two top T/C experts, Mike Bellm and Mike Sirois, have offered to explain the important features of Richard's rifle and the Encore platform. Bellm and Sirois were also kind enough to share many of their tips for building and tuning the TC Encore and similar break-open arms. Bellm explains how to accurize and tune the Encore, component by component, and Sirois describes his EDM chambering process and the benefits it affords for the Encore shooter.
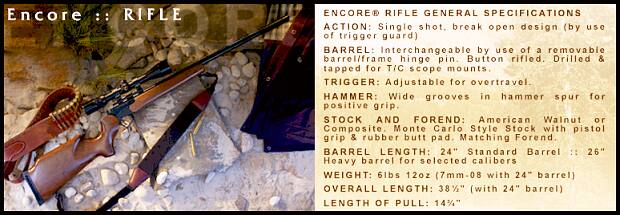
Bellm TCs, Inc., Encore/Contender Specialist
If you own an Encore, G2, or Contender, you should log on to the Bellm TCs website. There you'll find a host of information on the popular T/C break-open firearms, together with a complete range of T/C accessories including trigger kits, Headspace Dial Indicators, heavy-duty Locking Springs, oversized Hinge Pins, barrels and more. You'll also find a library of technical articles by Mike Bellm, covering tuning, accurizing, and maintenance of T/C arms. Mike is a talented smith and craftsman with decades of experience with break-open handguns and rifles. His enterprise is truly a one-stop shop offering all the key components you need to achieve peak performance with your Encore, G2, or Contender.
ADVANCED ENCORE TUNING << Click for Full Article Drawing on his many years of experience, Mike has been kind enough to author a very detailed article about Encores, explaining both how to set them up for best accuracy and how to modify and upgrade components for enhanced reliability. Click Here to read Mike's article, "How to Make the More Economical TC Encore Shooting System Work." |
Encore Accurizing and EDM Chambering by Mike Sirois I own and operate On Target Technologies, LLC. ("OTT"), a small business located in Dover, NH. I am a Journeyman Toolmaker by trade with strong Engineering and Mold-making background. My other business, MBM Company, designs and builds automation equipment for a variety of businesses. OTT was created to develop a variety of products for use with Encores and Contenders. Quickly this expanded to actually building custom barrels for a variety of actions. The first barrel built was a 45 Long Colt for the Contender in 2002. Incorporating a variety of design changes to make an ever more user-friendly assembly, everything is manufactured in-house with the exception of the barrel blank and locking bolts.
Chambering and Barreling for Optimal Accuracy In my opinion, the Encore can be very accurate if high-quality reloading components are used, and if the barrel assembly is precision-crafted with a chamber that precisely matches the ammunition. In addition, the lug must be sized and located just right to achieve best accuracy. Creating an optimal barrel assembly is one of our specialties at OTT. We treat that assembly as a precision piece of equipment that will actuate and operate in the same manner each and every time. OTT has devised quite a few methods to produce better barrel assemblies and more accurate rifles. The processes we use to build high-precision Encore/Contender barrel assemblies include Wire EDM, heat-treating, replacing certain stock components with upgraded pieces, and chambering via Conventional EDM (Electro Discharge Machining). During assembly we pay special attention to geometry and stress-avoidance. For example, during chambering the barrel is suspended via a magnetic V-block, precision-ground for squareness and perpendicularity. This way there is no stress to the barrel from clamping. (The only stress Richard's barrel saw was during profiling, TIG-welding the lug, and finally drilling and tapping the sight and fore-end mounting holes.)
Richard's 6BR barrel was made from an air-gauged Douglas 1:12" blank. As a model for the chamber, Richard supplied two (2) dummy rounds with the largest grain bullet he planned to shoot. He requested the neck clearance to be between .0005/.001" total. The top of the shoulder diameter and rear web area was held to .003" total. The barrel is 25" long, with a 1" straight taper, and an 11° target crown. The hinge pin hole was lapped to fit an oversize pin Richard supplied. Richard's dummy rounds (and his requested neck clearance) provided all of the information for the chamber. I use an optical comparator to measure key dimensions, such as the actual straight-line intersection point of the neck and shoulder. Finding the TRUE angle of the shoulder, I then note the transitional radius from the neck to the shoulder-angle junction. All of this is written down in a notebook for further calculations. Simple trigonometry is used to find the end points in relationship with the radius so that they can then be applied to the chamber's profile. That profile that is then used to manufacture the two electrodes (roughing and finishing), used to cut the chamber. The barrel is turned to 1" diameter, then cut to length. The crown of the bbl is cut utilizing a four-jaw chuck and the bore is indicated within .0005" TIR. I try to get as close to "0" as is possible. I think it matters with the crown.
Richard's barrel was treated and cut like every barrel produced by OTT, delivering a truly custom-chambered barrel that exactly matches Richard's ammunition. This, in turn, has produced a very accurate rifle. The patented EDM process allows custom chambering to be done very easily and with great precision. The process is stress-free. Moreover, since the electrode rotates while cutting, EDM guarantees a perfectly round hole which matches the cartridge exactly. Compared to using a conventional chamber reamer, EDM offers much more control over internal geometry. This allows me to refine the internal chamber profile.
The Barrel Lug--A Critical Component On Encores and Contenders, the barrel lug is key to accuracy. It must be precisely positioned and sized. The lug is manufactured complete prior to turning the barrel. Some businesses machine their lugs after welding to the barrel. By contrast, I machine lugs complete prior to welding so that the relationship of hinge-pin hole to locking bolt slot is the same on all lugs. Set screws are used instead of roll pins so that no hammer is needed to assemble or disassemble for later servicing. The hinge-pin hole is left .001" undersize from Wire EDM so that it can be lapped to size prior to fit-up. The lug is heat-treated complete and left slightly long for frame-gap grinding after welding. Once the barrel assembly has been ground to the ideal frame-gap dimensions and lug-finish thickness, it is ready for chambering. Finally, the lock-up is adjusted so that all the gun's barrels (when the gap is ground) will lock up the same and the customer should never have to adjust locking bolt heights.
EDM Machining--Milling on a Molecular Scale EDM is an automated process that can run unattended. It utilizes electricity to disintegrate everything in the electrode's path, imprinting the electrode's profile into the parent material. The machining takes place on a molecular scale via sparking action. The spark heats the grains and structure of the chamber wall beyond their critical temp in the gap. The removed metal is then carried away as smoke within a dielectric insulating fluid. Finish cuts can be as low as .001" per inch per side. The actual recast layer is less than .0001" after a finish-cut cycle, and is easily removed by lapping compound.
EDM chambering begins with production of specifically-sized electrodes. The electrodes are cut basically to include the throat length and a given lead-angle length. This area is left .001" undersize for later lapping to size, and also to remove as much material as possible. The electrodes are made of high-grade graphite to minimize wear. The finish electrode is usually the same size as the cartridge, but in Richard's case, due to his desired tight clearances, it was smaller than the actual neck of the cartridge. The electrodes are indicated for less than .001" TIR; .0005" or less is optimum. The bore centerline where the bullet is to sit has already been positioned with a probe and an electrically-finding center. The roughing electrode was set to the desired TIR and was positioned using a gauge block and the end of the barrel. The original notebook dimensions used for electrode manufacture are used again to program the depth stop on the EDM. Coolant to insulate the cut is provided from the muzzle end of the barrel. (The EDM is basically running in reverse, feeding the barrel downward on to the electrode.)
Setting the finish electrode is the same as the roughing, but we use a lower power setting to control the overburn from electrode to work-piece. The barrel when done is then indicated in a lathe in a four-jaw chuck again, so that the chamber can be finish-polished. Polishing is done with wooden chopsticks and two grades of lapping compound--one for roughing, one for finishing. This allows the recast layer of the cut to be smoothed up to enhance case extraction. This method cleans up the surface uniformly, avoiding the problems you can get with emery paper or a honing stone. At this point all that is left is hand-lapping the throat diameter and leade angle. One degree per side is the norm for taper. On Richard's barrel I also used a finish lap to ensure the neck diameter was to size and had no taper. After lapping was complete, I drilled and tapped the barrel for sights and fore-end, and then blasted the surface to prep for the final black-oxide finish.
Mike Sirois ("sih-roy") On Target Technologies, LLC.
|
Encore Trigger and Headspace Dial Indicator Photos Copyright © 2005 Mike Bellm All Rights Reserved. Thompson Center Studio photo with specifications Copyright © 2005 Thompson/Center Arms Co., Inc., All Rights reserved, used by permission. Fore-end photo Copyright © 2005 Ole Georgia Jim, All Rights Reserved, used by permission.All other content Copyright © 2005, 6mmBR.com, All Rights Reserved. No reproduction of any content without advanced permission in writing.
Topics: EDM, Electro Discharge Machining, Chambering, Accurizing, Thompson Contender, Thompson, Encore, Contender, Break-open, Rifle, pistol, AA 2230, V-Max, Silhouette, single-shot, switch-barrel, hunting, varmints, varminting, groundhog shooting, rifle accuracy, 6BR, 6mm BR, 6mm Norman, 6PPC, 22PPC, 220 Russian, 6mmBR, 6BR, 6 Dasher, .222 Remington, 17HMR, 17 Remington, 204 Ruger, 22 Hornet, .221 Fireball, 6.5mm, 7mm, Ackley Improved, stocks, Brown custom actions, stainless barrel, Encore, reloading, powder selection, case forming, fire-forming, Lapua Brass and Hornady bullets.
|